
From one person to another: our way of carrying out projects
References say more than a thousand words. The names of our customers are synonymous with the personal relationships that have grown over time among all project participants. This is just one reason why we, an established company for industrial control and automation technology, to this day are a trusted partner for many industries nowadays.
Our projects – technical details, here we go!
Date: 2023 to 2025
Contracting entity: BMW Plant Construction
End customer/site of installation: BMW Hungary (W15)
Project description:
- Entire electric planning (hardware construction, software project planning)
- Control cabinet construction
- Provision of control technology
- Assembly and installation
- Robot programming
- Virtual commissioning, physical system start-up
Technologies (excerpt):
- 21 pieces S7-1500 with CPU 1518F – PN/DP
- 21 pieces OC visualization with WinCC Unified on Beckhoff CP3224
- 51 pieces OP visualization with WinCC Unified on Beckhoff CP3224
- 95 pieces KUKA KRC5 industrial robots
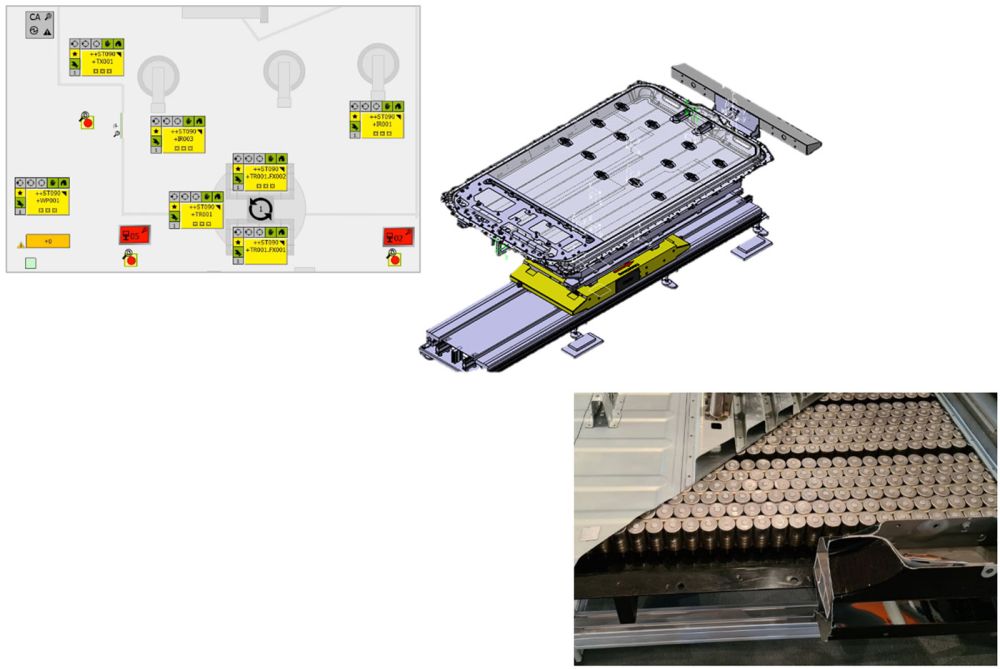
Date: 2023 to 2024
Contracting entity: BMW Group
End customer/site of installation: BMW Dingolfing
Plants such as:
- WU292/oven (refurbishment)
- WU292/press (refurbishment)
- WU293/oven (refurbishment)
- WU293/press (refurbishment)
Project description:
- Entire electric planning (hardware construction, software project planning)
- Control cabinet construction, air conditioning, and SEW inverter adjustment
- Provision of burner control units
- Assembly and installation
- Car body parts are hardened on two identical systems, WU292 and WU293. For this purpose, the cold-pressed components are heated in a continuous furnace and systematically cooled
- in a tool in the press. Measures to maintain the substance of the electrical components of the conveyor lines are being carried out at both plants. Cables and components are renewed,
- parts are brought up to date and recommissioned.
Technologies (excerpt):
- 8 pieces S7-400 with CPU 416
- 8 pieces Visualization Zenon 7.60
- 56 pieces Burner control units
- 20 pieces Rittal cooling systems Blue e+
- 60 pieces SEW inverter on MOVI-PLC
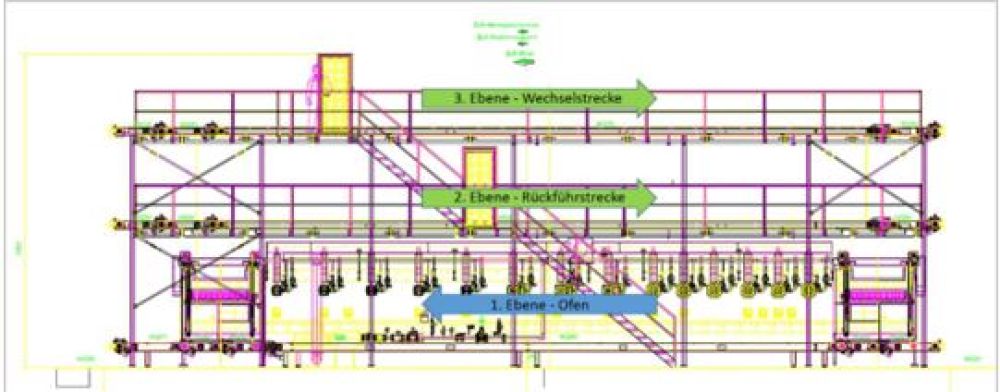
Date: 2023 to 2024
Contracting entity: TMS Turnkey Manufacturing Solutions GmbH
End customer/site of installation: BMW Dingolfing
Plants such as:
- Body carcass 1 (integration)
- Body carcass 2 (integration)
- Body carcass 3 (integration)
- Body carcass 3 – welding (integration)
- Side frame – inside (integration)
- Side frame – middle (integration)
- Side frame – outside (integration)
Project description:
- Entire electric planning (hardware construction, software project planning)
- Control cabinet construction
- Provision of control technology
- Assembly and installation
- Robot programming
- Virtual commissioning, physical system start-up
Technologies (excerpt):
- 18 pieces S7-1500 with CPU 1518F – PN/DP
- 18 pieces Visualization with WinCC on PC 677
- 35 pieces Visualization with WinCC on PC 477E
- 70 pieces Control units with WinCC visualization
- 76 pieces KUKA KRC4 industrial robots … in the body carcass range
- 60 pieces KUKA KRC4 industrial robots … in the side frame range
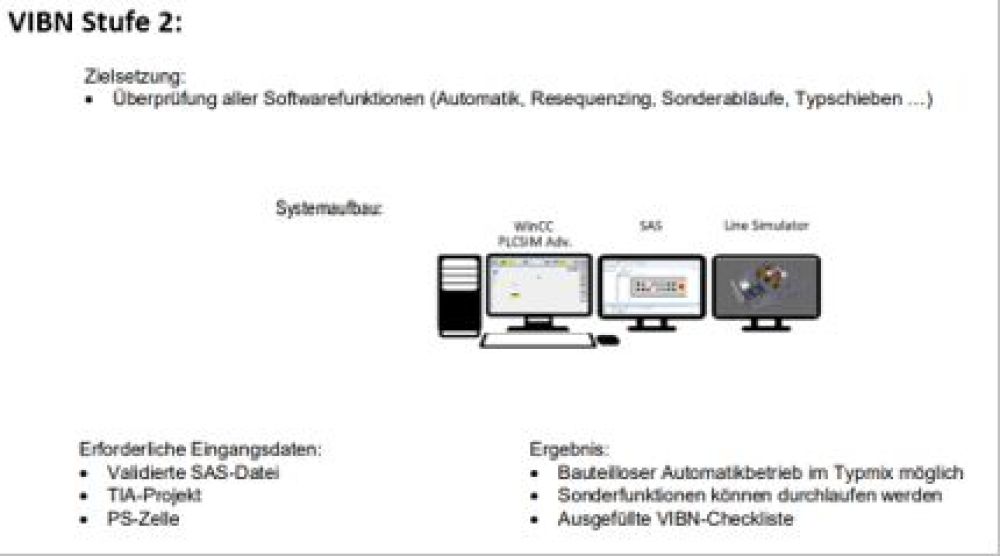
- Date: 2021 to 2023
- Contracting entity: BMW Plant Construction
- End customer/site of installation: BMW Regensburg
Plants such as:
- Body carcass 1, Body carcass 1 – AS, WL, HFR (integration)
- Body carcass 2, Body carcass 2 – AS (integration)
- Body carcass 3, Body carcass 3 – AS (integration)
- Roof system (integration)
- Front flap (new system)
- Measuring cells GOM (new system)
Project description:
- Entire electric planning (hardware construction, software project planning)
- Control cabinet construction
- Provision of control technology
- Assembly and installation
- Robot programming
- Commissioning
Technologies (excerpt):
- 28 piecesS7-400 with CPU 416
- 28 pieces Visualization with Zenon on PC 627
- 40 pieces Control units with Zenon visualization
- 235 pieces ABB IRC5 industrial robots (integration)
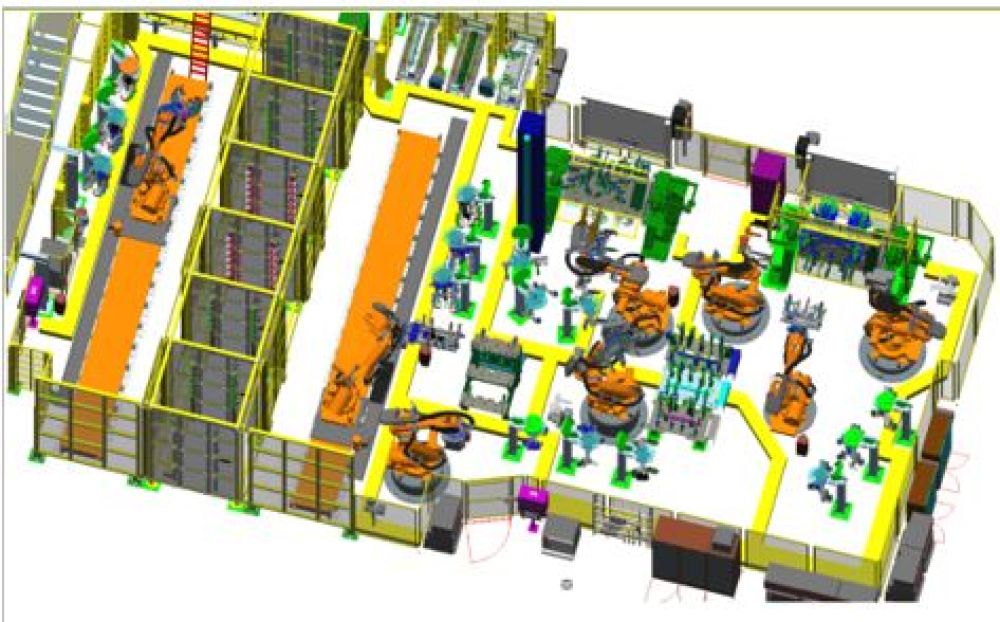
Date: 2019 to 2024
Contracting entity: BMW Plant Construction
End customer/site of installation: BMW Dingolfing
Plants such as:
- G60 – KG1, KG2, KG3, KG-AS, HFR, WL
- G60 – side frame inside, middle, outside
- G61 – KG1, KG2, KG3, KG-AS, HFR, WL
- G61 – side frame inside, middle, outside
- G32 – side frame inside, middle, outside
- G6x – roof system
Project description:
- Entire electric planning (hardware construction, software project planning)
- Control cabinet construction
- Provision of control technology
- Assembly and installation
- Robot programming
- Virtual commissioning, physical system start-up
Technologies (excerpt):
- 40 pieces S7-1500 with CPU 1518F – PN/DP
- 40 pieces Visualization with WinCC on PC 677
- 80 pieces Visualization with WinCC on PC 477E
- 100 pieces Control units with WinCC visualization
- 244 pieces KUKA KRC4 industrial robots … in the body carcass range
- 156 pieces KUKA KRC4 industrial robots … in the side frame range
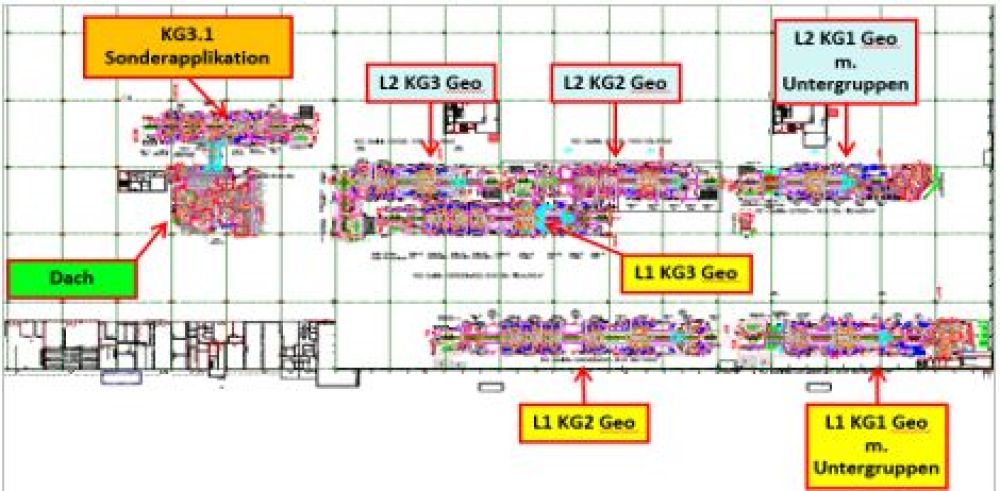
Date: 2019 to 2021
Contracting entity: BMW Plant Construction
End customer/site of installation: BMW Regensburg
Plants such as:
- Body carcass 1, Body carcass 1 – AS, WL, HFR (integration)
- Body carcass 2, Body carcass 2 – AS (integration)
- Body carcass 3, Body carcass 3 – AS (integration)
- Roof system (integration)
- Front flap (new system)
- Measuring cells GOM (new system)
Project description:
- Entire electric planning (hardware construction, software project planning)
- Control cabinet construction
- Provision of control technology
- Assembly and installation
- Robot programming
- Commissioning
Technologies (excerpt):
- 30 pieces S7-400 with CPU 416
- 30 pieces Visualization with Zenon on PC 627
- 50 pieces Control units with Zenon visualization
- 250 pieces ABB IRC5 industrial robots (integration)
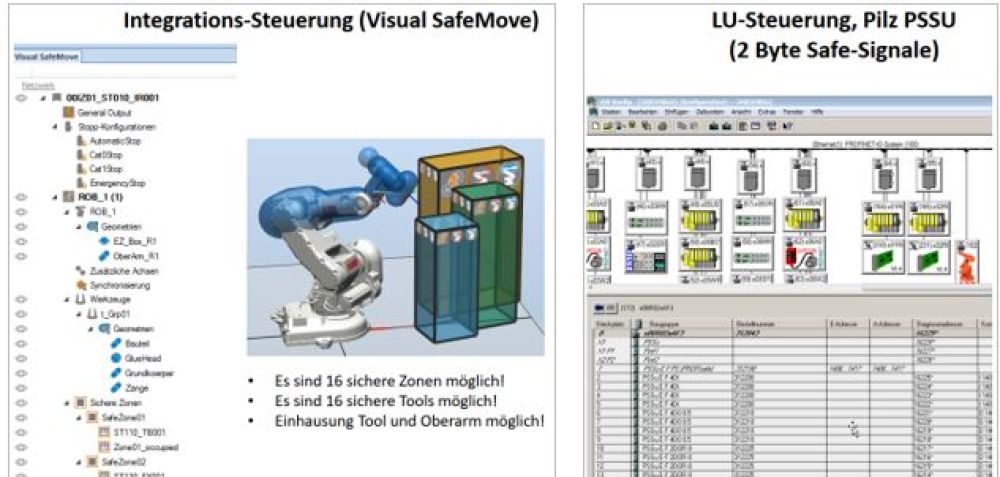
Date: 2019 to 2022
Contracting entity: BMW Plant Construction
End customer/site of installation: BMW München
Project description:
- Entire electric planning (hardware construction, software project planning)
- Control cabinet construction
- Provision of control technology
- Assembly and installation
- Robot programming
- Virtual commissioning, physical system start-up
Technologies (excerpt):
- 14 pieces S7-1500 with CPU 1518F – PN/DP
- 14 pieces Visualization with WinCC on PC 677
- 33 pieces Visualization with WinCC on PC 477E
- 15 pieces Control units with WinCC visualization
- 130 pieces ABB IRC5 industrial robots
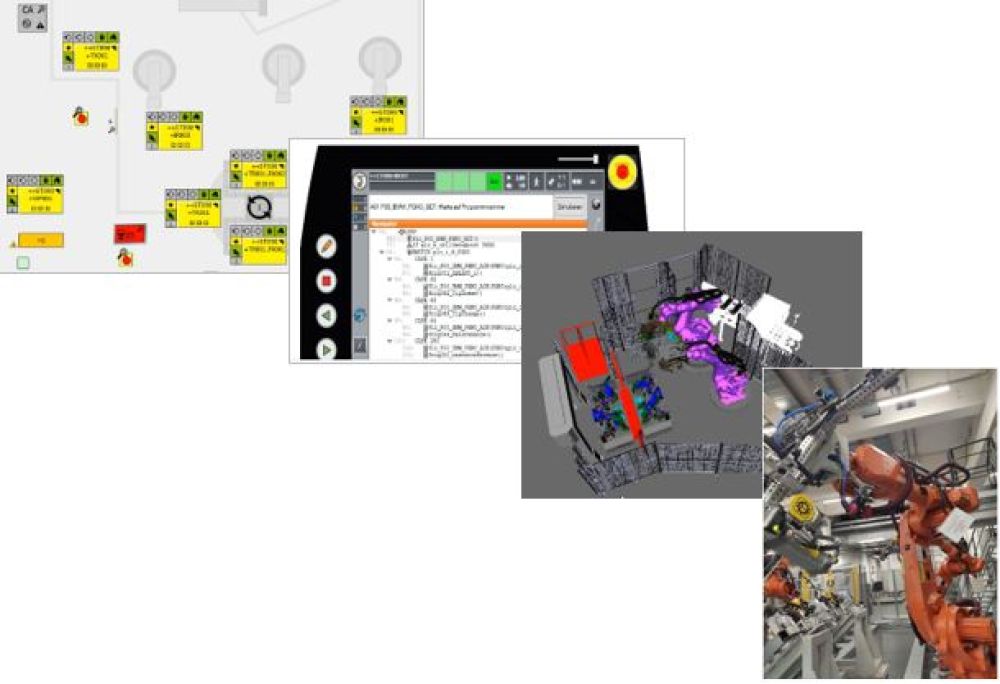
Date: 2019 to 2022
Contracting entity: BMW Plant Construction
End customer/site of installation: BMW Dingolfing
Plants such as:
- Body carcass 1 (integration)
- Body carcass 2 (integration)
- Body carcass 3 (integration)
- Body carcass 3 – welding (integration)
- Side frame – inside (integration)
- Side frame – middle (new systems)
- Side frame – outside (new systems)
Project description:
- Entire electric planning (hardware construction, software project planning)
- Control cabinet construction
- Provision of control technology
- Assembly and installation
- Robot programming
- Virtual commissioning, physical system start-up
Technologies (excerpt):
- 18 pieces S7-1500 with CPU 1518F – PN/DP
- 18 pieces Visualization with WinCC on PC 677
- 35 pieces Visualization with WinCC on PC 477E
- 70 pieces Control units with WinCC visualization
- 76 pieces KUKA KRC4 industrial robots … in the body carcass range
- 60 pieces KUKA KRC4 industrial robots … in the side frame range
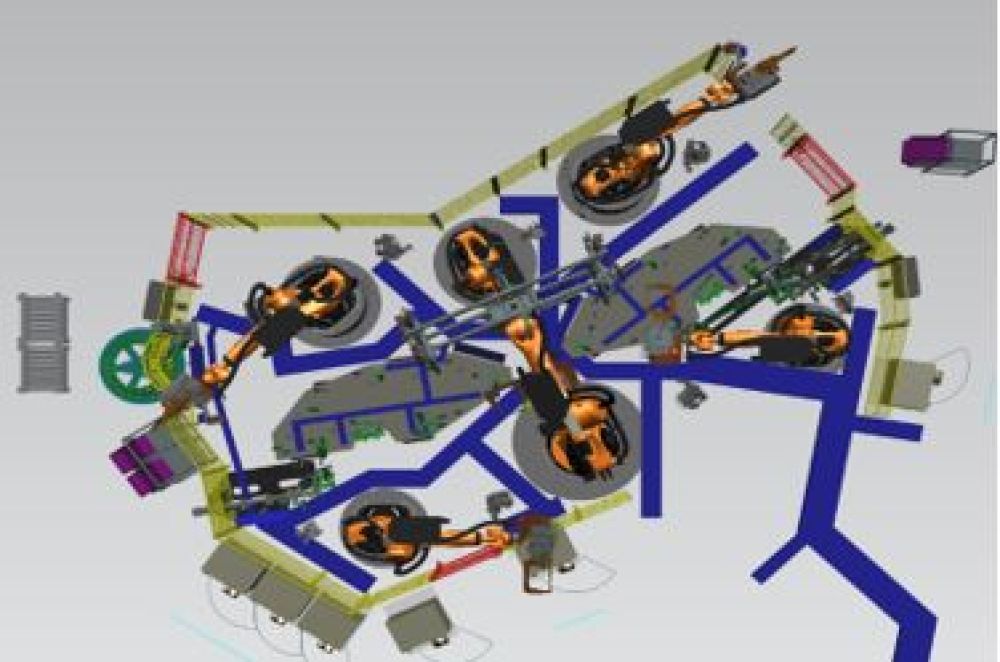
Date: 2019 to 2021
Contracting entity: BMW Plant Construction
End customer/site of installation: BMW Leipzig
Project description:
- Entire electric planning (hardware construction, software project planning)
- Control cabinet construction
- Provision of control technology
- Assembly and installation
- Robot programming
- Commissioning
Technologies (excerpt):
- 8 pieces S7-1500 with CPU 1518F – PN/DP
- 8 pieces Visualization with WinCC on PC 677
- 22 pieces Control units with WinCC visualization
- 53 pieces FANUC industrial robots
The scope also comprises the complete BestFit system, including hardware, software, engineering, and commissioning
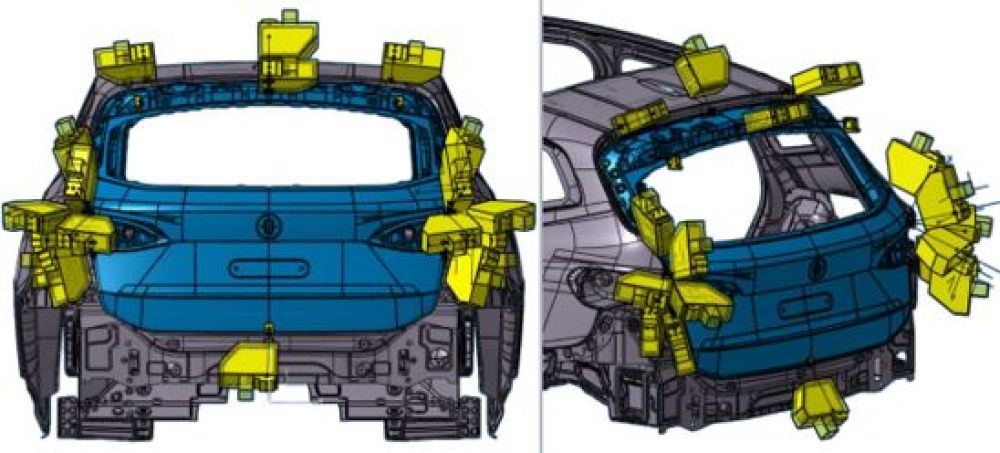
Date: 2019 to 2020
Contracting entity: BMW Plant Construction
End customer/site of installation: BMW Dingolfing
Project description:
- Entire electric planning (hardware construction, software project planning)
- Control cabinet construction
- Provision of control technology
- Assembly and installation
- Robot programming
- Virtual commissioning, physical system start-up
Technologies (excerpt):
- 5 pieces S7-1500 with CPU 1518F – PN/DP
- 5 pieces Visualization with WinCC on PC 677
- 9 pieces Visualization with WinCC on PC 477E
- 24 pieces Control units with WinCC visualization
- 39 pieces KUKA KRC4 industrial robots
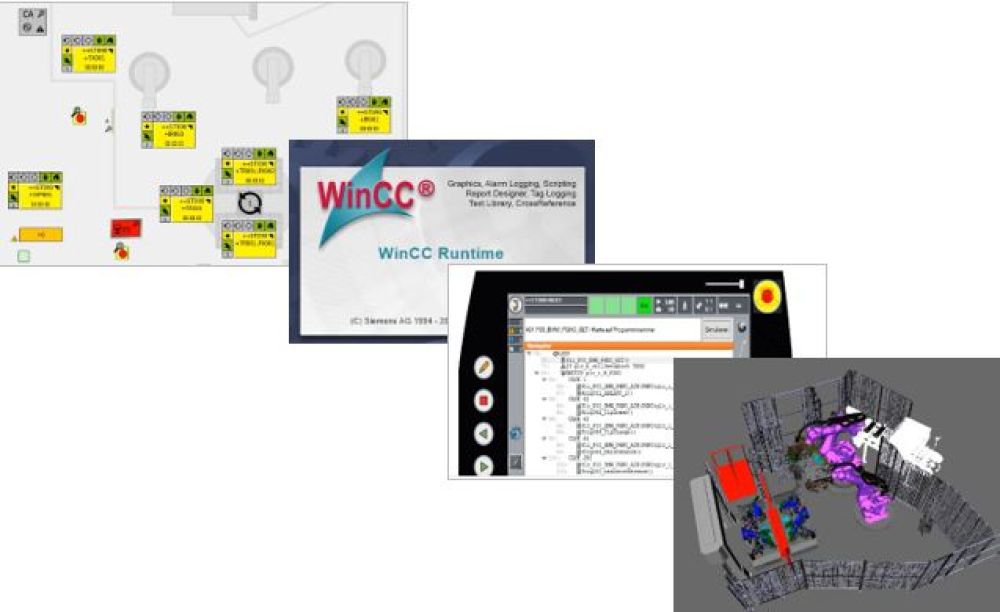
- Datum: 2018 to 2019
- Contracting entity: Emil Bucher GmbH
- End customer/site of installation: BMW Dingolfing
Plants such as:
- Assembly of left wheel housing
- Assembly of right wheel housing
- Assembly of front wall
- Entire front end
Project description:
- Entire electric planning (hardware construction, software project planning)
- Control cabinet construction
- Provision of control technology
- Assembly and installation
- Robot programming
- Commissioning
Technologies (excerpt):
- 9 pieces S7-1500 with CPU 1518F – PN/DP
- 9 pieces visualization with WinCC on PC 677D
- 18 pieces visualization with WinCC on PC 477E
- 14 pieces application PC677D
- 35 pieces control units with WinCC visualization
- 102 pieces KUKA KR C2/C4 industrial robots
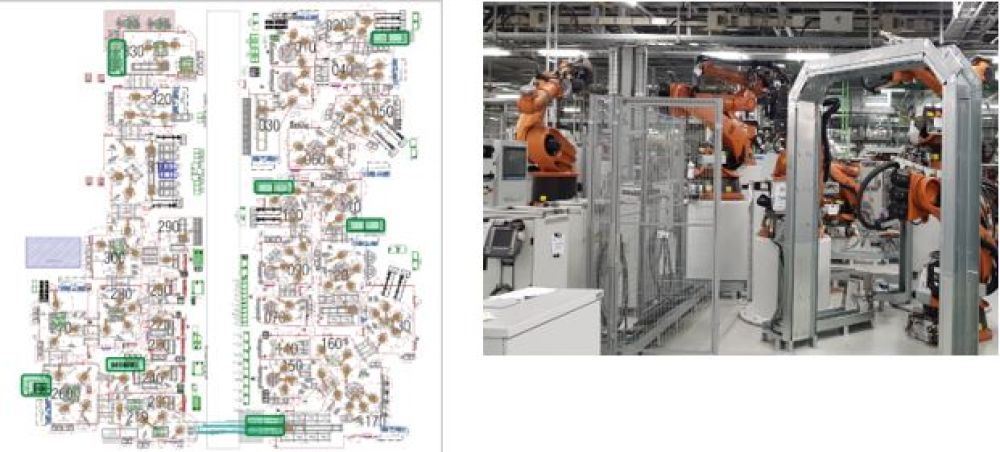
- Datum: 2017 to 2018
- Contracting entity: Emil Bucher GmbH
- End customer/site of installation: BMW Leipzig
Project description:
- Entire electric planning (hardware construction, software project planning)
- Control cabinet construction
- Provision of control technology
- Assembly and installation
- Robot programming
- Commissioning
Technologies (excerpt):
- 2 pieces S7-1500 with CPU 1518F – PN/DP
- 4 pieces visualization with WinCC on PC 677
- 5 pieces control units with WinCC visualization
- 20 pieces FANUC industrial robots
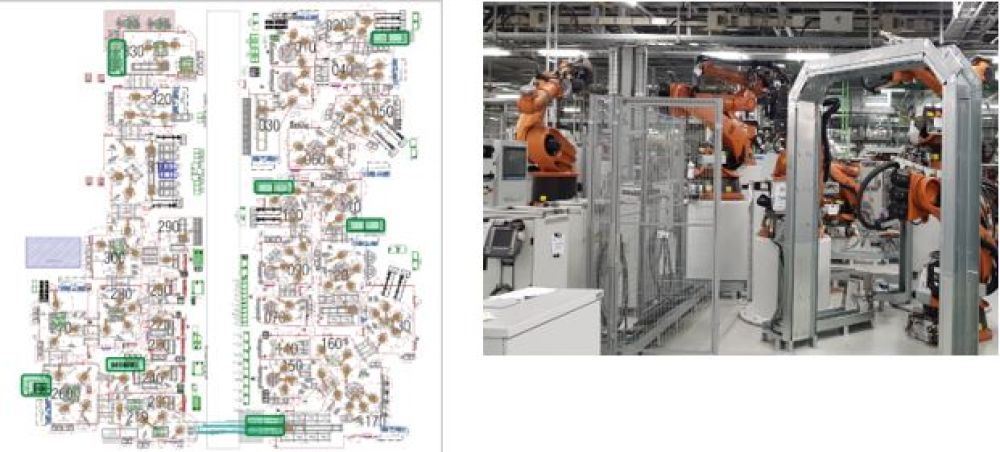
Date: 2022 to 2023
Contracting entity: Esypro
End customer/site of installation: BMW Dingolfing W02.10
Project description:
- Entire electric planning (hardware construction, software project planning)
- Control cabinet construction
- Provision of control technology
- Assembly and installation
- Virtual commissioning, physical system start-up
A conveyor system was installed to supply the wishbones and tie bars to the axis production assembly line. The components are hooked into workpiece carriers according to type in batch sizes at two feeding points and stored by variety in approx. 60 storage lanes. According to the current sequence, the production control system issues a call-up, whereby the components are retrieved from the storage in sequence. They are conveyed to the assembly stations via an intermediate level by means of a lifter. After removal, the empty workpiece carriers are conveyed back to the feed stations. Data handling is realized via RFID data carriers and barcodes.
Technologies (excerpt):
- 1 piece S7-1500 with CPU 1518F – PN/ DP
- 1 piece OC visualization with WinCC TIA on Beckhoff CP3224
- 7 pieces OP visualization with WinCC TIA on Beckhoff CP3224
- SEW MOVIFIT technology version
- Murr MVK I/O modules
- Siemens ET200SP and ET200Pro I/O modules
- Automatic barcode reader and hand scanner
Date: 2023 to 2025
Contracting entity: HORIBA
End customer/site of installation: BMW Aschheim
Project description:
- Planning (hardware construction, software project planning)
- Control cabinet construction
- Supply of new subdistribution boards, control cabinets, and human interfaces
- Assembly and installation
In the course of the new construction of 6 chassis dynamometers, we received the partial order to develop a new human interface and the visualization. The operating concept, which had become outdated, was to be renewed and converted to a modern concept with a promising future. The human interface is used for the central control and visualization of each test stand. In the first step of the project, 7 human interfaces are built, followed by 9 more in the second step, which are built and delivered. The visualization takes place via a server-client system with WinCC Unified V18.
Technologies (excerpt):
- 16 subdistribution boards/cabinets with S7-1516F/S7-1515F CPU
- 16 pieces human interfaces with ET200SP
- WinCC Unified V18
- TIA V18
Date: ongoing
Contracting entity: BMW
End customer/site of installation: BMW FIZ
Project description:
We are continuously renovating, maintaining, expanding and adjusting the existing lighting and blind control systems. A central control system was implemented to consolidate the building control system in the control center. Various external control systems are supplied with central control commands via the control center and monitored. A visualization enables the central control with switch-on and switch-off commands, which can be adjusted individually per building/floor if required.
Technologies (excerpt):
- >50 pieces Siemens S7-300 control systems in different designs
- >300 pieces WAGO I/O Profibus interfaces 750-xxx
- ~10 pieces Vipa small control systems 200V series
- 2 pieces Siemens 319F/1516F as central PLC in the control center
- 1 piece Comfort Panel TP2200 as central visualization
- ~30 pieces Touch Panels TP177B/A
- >200 pieces WAGO control systems in different designs
- KNX control systems
- WinCC Advanced V17
- TIA V17
- WinCC flexible 2008
- Step 7 V5.5
- WAGO light management software
- WAGO main distributor software
- KNX ETS5
Date: 2023 to 2024
Contracting entity: BMW
End customer/site of installation: BMW subsidiary
Project description:
In the course of renovation work, the lighting in the BMW branch is being renewed. This serves as a prototype for other branches. One of our responsibilities is the programming of the new lighting. New lighting distributors and new lighting fixtures are being installed. The operation is carried out via portable and commercially available tablets.
Technologies (excerpt):
- 3 pieces WAGO control systems with light management software
- > 600 Dali lamps
- 3 pieces tablets with WAGO visualization
Date: ongoing
Contracting entity: ERS-Elektrotechnik
End customer/site of installation: BMW FIZ
Project description:
We are continuously maintaining, expanding, and adjusting the existing monitoring control systems. These are used for the permanent monitoring of different measuring signals (temporary I/Os, currents). To record the signals, various PLC control systems are used, which collect and evaluate the measured values. The control systems are centrally visualized via a WinCC system, and an ACC system provides an operating status display and error alarm. In addition, energy meters are evaluated. Recirculating air-cooling units are centrally controlled for each smoke section. The control serves to provide the IT equipment with constant cooling, with the goal of using as little energy as possible.
Technologies (excerpt):
- ~40 pieces Siemens S7-300 control systems in different designs
- 1 piece Comfort Panel TP2200 as central visualization for energy measuring
- ~10 pieces Touch Panels TP177B/A
- WinCC Advanced V17
- WinCC flexible 2008
- Step 7 V5.5
- WinCC V7.x
Date: 2022 to 2023
Contracting entity: ICT
End customer/site of installation: BMW Spartanburg
Project description:
- Planning (hardware construction, software project planning)
- Control cabinet construction
- Supply of new subdistribution boards, control cabinets, and human interfaces
- Assembly and installation
- Software and commissioning
- Disassembly of old chargers
The final work on the production cars is carried out in an existing finishing line. To ensure that the 12VDC battery does not run down, it is possible to use external chargers to maintain or recharge the capacity. The existing system had to be adapted due to a new vehicle type. In the course of this work, the battery-charging concept was completely revised. A new EMS system was installed above the production line. This made it possible to provide the worker with battery chargers simultaneously with the car. A new control system was installed, which communicates with the carriers via a CAN bus and tracks them to within a few millimeters using a barcode positioning system. The track (approx. 300m) includes several switches and a repair track with maintenance jack. After successful implementation, the old battery technology was dismantled.
Technologies (excerpt):
- S7-1500 with CPU 1518F – PN/DP
- 1 piece OC visualization with WinCC TIA on Beckhoff CP3224
- 1 piece OP visualization with WinCC TIA on Beckhoff CP3224
- Vahle technology version
- SEW drives
- Siemens ET200SP and ET200Pro I/O modules
Date: 2023 to 2024
Contracting entity: DS AUTOMOTION GmbH – Linz /Austria
End customer/site of installation: BMW Spartanburg
Project description:
- Planning (hardware construction, software project planning)
- Control cabinet construction
- Supply of new subdistribution boards and human interfaces
- Assembly and installation
- Software and commissioning
- Disassembly of the existing system
In the course of an expansion of the final assembly, the existing plant must be moved and expanded. The AGVS will be moved in several steps and expanded according to construction progress. In addition, the general contractor also delivers other vehicles that we provide. Due to the increased power requirements, new cabinets need to be built and installed. New panels are used for the visualization. The software has to be changed and put into operation depending on the step and track. Our scope includes the complete disassembly and reassembly of electrical components.
Technologies (excerpt):
- S7-1500 with CPU 1518F – PN/DP
- 1 piece OC visualization with WinCC TIA on Beckhoff CP3224
- 1 piece OP visualization with WinCC TIA on Beckhoff CP3224
- Vahle technology version
- SEW drives
- Siemens ET200SP and ET200Pro I/O modules
Date: 2022 to 2023
Contracting entity: MBN
End customer/site of installation: BMW Spartanburg
Project description:
- Planning (hardware and software project planning)
- Disassembly and installation
- Software and commissioning
- Robot programming
- Disassembly of a system
Due to the discontinuation of a model and the introduction of a new type, the marriage had to be adjusted in the final assembly. As one of the existing systems was no longer needed, it was removed from the control system and uninstalled. In return, a new type was integrated into the remaining systems. This required, among other things, completely new procedures for the robots, screwdrivers, and in the process. Over the course of the years, the existing systems had been incorporated with a wide variety of standards and technologies and had to be individually adapted.
Technologies (excerpt):
- S7-1500 with CPU 1518F – PN/DP
- S7-400
- WinCC Tia with PCs, TPs
- Various robots
Date: 2020 to 2023
Contracting entity: DS AUTOMOTION GmbH – Linz /Austria
End customer/site of installation: BMW Dingolfing (W2.20)
Project description:
- Entire electric planning (hardware construction, software project planning)
- Control cabinet construction
- Provision of control technology
- Assembly and installation
- System commissioning
Technologies (excerpt):
- 1 piece S7-1500 with CPU 1518F – PN/ DP
- 2 pieces OC visualization with WinCC TIA V14 on Staudinger 0C-9-22-677D-V04/ EKS
- 2 pieces OP visualization with WinCC TIA on Staudinger OP-9-22-477E-V04/ EKS
- 8 pieces access points for Wi-Fi coverage (communication with vehicles)
- 5 pieces Loop 1 vehicles for the transport and assembly of the high-voltage storage systems (HVS)
- 19 pieces Loop 2 vehicles (exclusively manual workstations) with lifting and swiveling unit for the transport and assembly of the high-voltage storage units
Process description:
The central control system developed by Kocher for the automated guided vehicle system (AGVS) carries out not only the data management with the hall master control system of the end customer (from order data preview to error messages), but also all process-relevant orders of the vehicles through the robot cells and manual processing stations.
The master controller with its own Wi-Fi communication is the heart of the entire plant workflow.
It controls and monitors the process from the transmission of order data (marriage) throughout the production line at all station controls.
The production line is designed for the output of 30 HVS per hour and is divided into two areas.
Loop 1 with 65 vehicles and a mix of manual and automatic stations.
Loop 2 with 19 vehicles and manual stations only. These vehicles are equipped with a lifting and swiveling unit, which, after preselection for each station, enables targeted alignment and an ergonomic working position.
In a transfer station, the workpiece carriers with the partial body of the HVS are transferred alternately/step by step between Loop 1/2. The order data is transferred from the source vehicle to the new target vehicle in each case, so that communication between the vehicles and the stations is ensured for a reliable process.
A visualization interface allows, for example, input for the adjustment of parameters, HVS ident numbers, process dial-in/dial-out. All processes, positions of the vehicles and the on-board swivel devices, interface overviews to station and vehicle controls, and error messages are displayed.
In addition to the standard process sequences, emergency strategy concepts are implemented according to customer requirements.
Date: 2023 to 2024
Contracting entity: DS AUTOMOTION GmbH – Linz /Austria
End customer/site of installation: BMW Dingolfing (W2.20)
Project description:
- Entire electric planning (hardware construction, software project planning)
- Control cabinet construction
- Provision of control technology
- Assembly and installation
- Virtual commissioning, physical system start-up
Technologies (excerpt):
- 1 piece S7-1500 with CPU 1518F – PN/ DP
- 1 piece OC visualization with WinCC Unified on Beckhoff CP3224-2003-0020
- 2 pieces OP visualization with WinCC Unified on Beckhoff CP3224-2001-0020
- 3 pieces access points for Wi-Fi coverage (communication with vehicles)
- 45 pieces vehicles with swiveling unit and workpiece carrier for the transport and assembly of the high-voltage storage systems (HVS)
Process description:
The central control system developed by Kocher for the automated guided vehicle system (AVGS) carries out not only the data management with the hall control system of the end customer (order data preview to error messages), but also all process-relevant orders of the vehicles through the robot cells and manual processing stations.
The master controller with its own Wi-Fi communication is the heart of the entire plant workflow. It controls and monitors the process from the transmission of order data (marriage) throughout the production line at all station controls.
A visualization interface allows, for example, input for the adjustment of parameters, HVS ident numbers, process selection/deselection. All processes, positions of the vehicles and the on-board swivel devices, interface overviews to station and vehicle controls, and error messages are displayed.
In addition to the standard process sequences, emergency strategy concepts are implemented according to customer requirements.
Datum: 2023 to 2024
Contracting entity: DS AUTOMOTION GmbH – Linz /Austria
End customer/site of installation: AGCO Fendt – Marktoberdorf
Project description:
- Entire electric planning (hardware construction, software project planning)
- Extension of control cabinet construction
- Provision of control technology for the extension works
- Assembly and installation
- System commissioning
Technologies (excerpt):
- 1 piece S7-414F-3PN/DP
- 4 pieces MP277 10“ TOUCH
- 10 pieces access points for Wi-Fi coverage (communication with vehicles)
- 30 pieces vehicles for transport and setup of the tractors (combustion engines and e-tractors)
Process description:
The assembly line was adapted for the integration of the new electric vehicle (E124P series) into the final assembly of tractors in Marktoberdorf. The automated guided vehicle system (AGVS) ejects the vehicles with bodies for electric tractors from the existing production line so that the high-voltage assembly and testing processes can be carried out in a new, separate hall area. The electric tractors are then fed back into the existing production line. Of a maximum of four workstations in the new section, two will initially be fully integrated.
The central control system developed by Kocher for the AVGS carries out not only the data management with the hall control system of the end customer (order data to error messages), but also all process-relevant orders of the vehicles through the processing stations. The master controller with its own Wi-Fi communication is the heart of the entire plant workflow. It controls and monitors the process throughout the entire production line at all station control points.
For instance, a visualization interface allows entries to be made to adjust parameters and select/deselect processes. All processes, positions of the vehicles and overviews of interfaces to station and vehicle controls as well as error messages are displayed.
In addition to the standard process sequences, emergency strategy concepts are implemented according to individual requirements.
The projects mentioned above are just a selection from the last years. We are happy to provide you with further references – please don't hesitate to contact us!
Are you looking for modern control technology solutions?
Let us convince you in a personal conversation! Arrange an appointment with us right away: